Verzinktes hält. Ein Leben lang.
Das Tauchfeuerverzinken ist ein kostengünstiges, sehr wirksames Korrosionsschutzverfahren, mit dem Bauteile häufig "lebenslang" vor Rost geschützt werden können.
Schutzdauern* exemplarisch ausgewählter Bauteile | ||||
Bauteil | Material- dicke | Mittl. Zink- schichtdicke | Umgebung (innen/außen) |
Schutzdauer |
Geländer | 3 mm | 60 μm | in geheizten Räumen | > 100 Jahre |
Gitterrost | 2 mm | 55 μm | in nicht geheizten Räumen / in ländlicher Umgebung | > 35 Jahre |
Zaun | 5 mm | 80 μm | feuchte Produktionsräume / Stadt- & Industrieatmosphäre | > 35 Jahre |
Vordach | 6 mm | 90 μm | Chemieanlagen / industrielle Bereiche, Küstenatmosphäre mit mäßiger Salzbelastung | > 20 Jahre |
*Angaben basieren auf den in der Norm DIN EN ISO 14713-1:2010-05 (Zinküberzüge – Leitfäden und Empfehlungen zum Schutz von Eisen- und Stahlkonstruktionen vor Korrosion, Teil 1: Allgemeine Konstruktionsgrundsätze und Korrosionsbeständigkeit) genannten Abtragswerten. |
Im Unterschied zu anderen Verfahren findet beim Feuerverzinken zwischen dem Beschichtungsstoff (Zink) und dem Werkstoff (Stahl) eine chemische Reaktion statt, während der sogenannte Legierungsschichten entstehen: Zink und Stahl gehen eine innigliche Verbindung ein. Dadurch entsteht die für das Feuerverzinken typische, mechanisch belastbare Oberfläche: ausgezeichnet in punkto Haftung, Abriebfestigkeit und Unempfindlichkeit gegen Anstoßen.
Doch auch in ästhetischer Hinsicht kann die Feuerverzinkung häufig überzeugen. Immer vorausgesetzt dessen Anwendungsgrenzen werden beachtet.
Das Gelingen des Feuerverzinkungsprozesses hängt sowohl vom Material des Werkstücks als auch dessen konstruktiver Gestaltung ab, die deshalb Gegenstand normativer Regeln sind.
Bitte machen Sie sich unbedingt mit deren wichtigsten Vorgaben vertraut, wozu wir Ihnen neben den Technischen Hinweisen auch unseren nebenstehenden Videofilm empfehlen!
Technische Hinweise
Generell:
Falls Sie sich über die Eignung Ihres Bauteils zum Feuerverzinken im Unklaren sind, empfehlen wir Ihnen, eine Probeverzinkung durchführen zu lassen! Schwierige Fragen, vor allem hinsichtlich der konstruktiven Gestaltung, der Aufhängemöglichkeit sperriger Konstruktionen oder Ähnlichem, können ggf. gemeinsam mit unserem Außendienstmitarbeiter geklärt werden. Bitte sprechen Sie uns hierauf an.
Materialauswahl
Weil das Feuerverzinken ein chemischer Prozess (zwischen Eisen und Zink) ist, sind die Bestandteile des Stahls und dessen Herstellungsverfahren von eminenter Bedeutung für das Verzinkungsergebnis. Vor allem die chemischen Elemente Silizium und Phosphor gelten als kritisch für die Reaktionsgeschwindigkeit und infolge dessen den Zinkschichtaufbau. Deshalb sind sowohl Aussehen als auch die mechanischen Eigenschaften der Zinkschicht-Oberfläche durch ihren Einfluss bedingt: Im ungünstigen Fall können sich dicke, unebene bis borkige Schichten bilden, die leicht abplatzen.
Einfluss von Silizium und Phosphor auf Zinkschicht:
Stahlsorte | Silizium + Phosphor | Aussehen des Zinküberzugs |
Si-/P- arme Stähle | < 0,03 % | Silbrig glänzend, niedrige Schichtstärke, Zinkblume |
Sandelin - Stähle | 0,03 % bis 0,13 % | Grau, z. T. grießig, hohe Schichtdicke |
Sebisty - Stähle | 0,13 % bis 0,28 % | Silbrig glänzend bis mattgrau, mittlere Schichtdicke |
Si-/P- reiche Stähle | > 0,28 % | Mattgrau, hohe Schichtdicke |
Quelle: Arcelor Commercial Section S. A., 66 rue de Luxembourg, L-4221 Esch-sur-Alzette
Deshalb ist bei der Bestellung von Stahlprofilen stets deren Eignung zum Feuerverzinken gemäß DIN EN 10025-2, Tabelle 1 (Klasse 1 o. 3) zu fordern!
Die Eignung zur Feuerverzinkung von Bauelementen aus Gusseisen oder gepresstem Stahlpulver (Zierelemente) sind aufgrund ihrer unbekannten Provenienz (chemische Zusammensetzung, Herstellungsweise, Verunreinigungen, Porosität, Lufteinschlüsse, etc.) stets ungewiss. Für diese Elemente ist eine Probeverzinkung (eines Einzelteils) anzuraten!
Stabilität
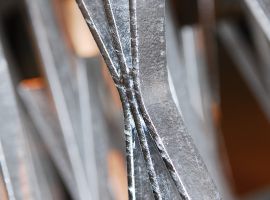
Weil das Werkstück in heißes, schmelzflüssiges Zink getaucht wird, muss das gesamte Bauteil in sich genug Stabilität besitzen, um
- an 2 - 3 Punkten aufgehängt zu werden, ohne sich, bei halbierter Dehnungsgrenze (450° C), dauerhaft zu verformen und
- der Wärmebeaufschlagung stand zu halten.
Gerade ältere, fragile Bauteile (korrodierte Ziergitter, dünne Rohre u. dgl.) besitzen häufig nicht mehr die hierzu nötige Festigkeit. Diese können dann nur noch spritzverzinkt werden.
Aufhängepunkte
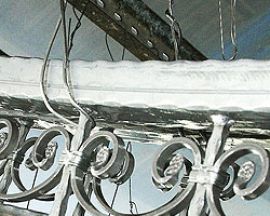
Die Aufhängepunkte sind so zu wählen, dass
- diese gemeinsam mind. das dreifache Bauteilgewicht tragen können,
- in der Hängeposition sämtliche Bauteilflächen ggü. der Waagerechten um mind. 20° geneigt sind (wegen der sich bildenden Ablaufnasen und Zinkverdickungen)
- die unvermeidlichen Zink-Klebestellen weder die Bauteil-Funktion noch dessen Ästhetik beeinträchtigen.1
Wenn kleinere Teile (< 250 mm lang und < 2 kg schwer) bauartbedingt keine Aufhängemöglichkeit bieten oder eine gleichmäßig glatte und feste Oberfläche aufweisen sollen, insbesondere um deren Bohrungen passfähig zu halten, dann können diese Teile schleuderverzinkt werden.
1 Bitte weisen Sie uns spätestens bei Auftragserteilung explizit auf die Funktionsflächen und die "wesentlichen" Flächen hin, die erhöhten ästhetischen Ansprüchen genügen müssen!
Oberfläche
Oberflächen-Vorbereitung
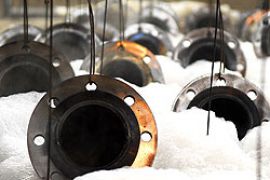
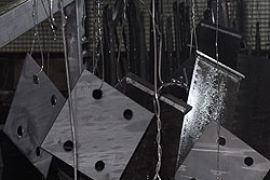
Für das Feuerverzinken ist eine metallisch reine Stahloberfläche unabdingbar! Während übliche Rost und Zunderschichten unproblematisch sind - weil diese von den Vorbehandlungsmedien der Verzinkerei entfernt werden - darf der Stahloberfläche nichts Fremdes anhaften, wie
- 1. Beschichtungen: (Signier-)Farben und Lacke, Klebereste (Etiketten)
- 2. Zinkschichten (auf Beschlägen, Schrauben etc.)*
- 3. Schweißsprays, silikonhaltige Hilfsstoffe aus der Stahlbearbeitung
- 4. zähflüssige Öle und Fette
- 5. Grate, Schweiß- u. Brennschlacken, Schweißspritzer
- 6. Späne, Strahlmittelreste
zu 1.
Farbschichten können von uns durch Sandstrahlen oder chemisches bzw. thermisches Entlacken entfernt werden. Dabei ist ein Entlacken immer dann vorzuziehen, wenn Hohlkörper von innen beschichtet sind oder Farbe sich in schwer zugänglichen Stellen befindet (alle nicht gerundete Körperecken, Falzkanten, Materialüberlappungen, Spalte usw.). Anderenfalls verbrennen die (manchmal nicht sichtbaren!) Farbreste in der Zinkschmelze und hinterlassen schwarze Fehlverzinkungsstellen.
Klebereste lassen sich i. d. R. einfach mit einem Klebstoffentferner (auch bei uns im Verkaufssortiment bestellbar) beseitigen. Gerne übernehmen wir das für Sie.
zu 3.
Trotz der Versprechungen der Schweißspray-Hersteller ("silikonfrei"), führen solche Trennmittel immer wieder zu Fehlverzinkungsstellen. Abhilfe schafft hier häufig nur ein ausreichend starker Schweißstrom.
zu 5.
Brennschnittkanten (mit Sauerstoff - Acetylen, Plasma oder Laser) sollten vor dem Verzinken überschliffen werden (0,1 mm sind ausreichend). Anderenfalls ist eine Behinderung der Eisen-Zink-Reaktion in diesem Bereich nicht auszuschließen, mit der Folge einer nur dünnen und schlecht haftenden Zinkschicht.2
Sorgen Sie zudem dafür, dass die scharfkantigen (Laser-) Schnitte gebrochen werden, weil an solchen Ecken die Haftung sowohl von Zinkschichten als ggf. auch Farbschichten vermindert ist, diese also leicht abplatzen.
Bedenken Sie bitte, dass das Verzinken i. d. R. nicht zu einer Einebnung der Oberfläche führt. Gerade Schweißnähte und Bereiche mit lokal höheren inneren Spannungen können den Zinkaufbau befördern und zeigen dann in diesen Bereichen Schichterhebungen.
Schalen und Schuppen des Grundwerkstoffes, die aus Werkstoffüberschiebungen beim Walzen der Stahlprofile resultieren, erscheinen nach dem Verzinken häufig als picklige Oberfläche.
*Sind nur lokal verzinkte Stellen vorhanden, kommt alternativ zum aufwändigen Entzinken des gesamten Bauteils dessen Schutz mit Anti-Zink-Paste infrage, ggf. zusammen mit einer Nachbehandlung mit Zinkstaubfarbe.
Örtlicher Schutz vor Zinkauftrag
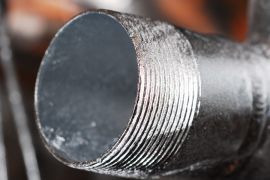
Sollen nicht alle Bereiche eines Bauteils verzinkt werden, z. B. Gewindeteile, Scharniere, Passflächen u. dgl. können diese mit Anti-Zink-Paste geschützt werden. Vergewissern Sie sich, dass die Paste ausreichend durchgetrocknet ist (mind. 24 h), bevor Sie uns diese Bauteile übergeben.
Nachträgliche Ausbesserung von Fehlstellen 1
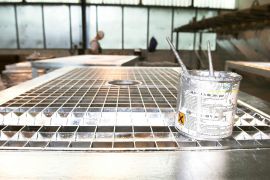
Normgerecht ist eine Ausbesserung mit:
- - Zinkstaubfarben ( normgerechtet nach IS0 3549)
- - Zinkloten
- - thermischen Spritzen mit Zink
Allerdings darf die Summe aller Fehlstellen 0,5 % der Gesamtoberfläche nicht überschreiten. Und die einzelne Fehlstelle darf nicht größer als 10 cm2 sein. Die Mindestschichtstärke der ausgebesserten Fehlstelle muss einheitlich 100 µm betragen.2
Dabei ist zu beachten, dass die Ausbesserungsfläche auch den intakten Zinkschicht-Randbereich überdecken muss, also stets größer als die eigentliche Fehlstelle ist. Soll das verzinkte Bauteil anschließend noch beschichtet werden, ist das Ausbesserungsmittel hierauf abzustimmen. Für eine Pulverbeschichtung muss es der erhöhten thermischen Belastung standhalten und elektrisch leitfähig sein!
1 Stellen, an denen der Grundwerkstoff keinen Zinküberzug aufweist.
2 Ausgenommen sind die Innenflächen nicht begehbarer Hohlkonstruktionen.
Hohlräume
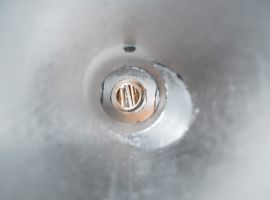
Hohlprofile sind an beiden Enden so großzügig zu öffnen, dass unten das Zink und oben die Luft zügig ein- und austreten kann. Die Öffnungen müssen sorgfältig an den obersten und untersten Punkten eingebracht werden, weil sonst das Zink nicht in alle Ecken vordringen kann (Luftblasen). Hinsichtlich der erforderlichen Lochgrößen und deren genauer Positionierung bitten wir die Angaben unseres Merkblattes zu beachten, insbesondere dessen Lochtabelle.
Merkblatt: Feuerverzinkungsgerechtes Konstruieren (PDF)
Nach dem Verzinken können diese Löcher mittels Kunststoff-Stopfen wieder verschlossen werden.
Sehr kleine Öffnungen (< 2 mm), z.B. Spalten zwischen überlappenden Profilflächen und Lunker in Schweißnähten, sind zu vermeiden. Hierin können sich Salzsäure-Reste einnisten, die im Laufe der Zeit die Zinkschicht von innen her zersetzen und schließlich als rostbraune Fahne austreten.
Verzugsgefahr
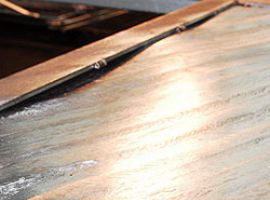
Während das zu verzinkende Bauteil in die 450 °C heiße Zinkschmelze getaucht wird, muss es erheblichen Ausdehnungskräften standhalten - u.z. ohne sich dabei plastisch zu verbiegen! Diese Gefahr ist dann am geringsten, wenn sich das Bauteil gleichmäßig erwärmt. Hierzu ist das Einhalten zweier Voraussetzungen vonnöten:
- 1. Das heiße Zink muss in alle Hohlräume schnell eindringen können, damit das Bauteil zügig untergeht. Deshalb sollten insbesondere lange Hohlprofile größere Bohrungen erhalten als in der Lochtabelle angegeben.
- 2. Die einzelnen Bauteilprofile müssen vergleichbare Materialdicken haben, damit die Profile sich ähnlich schnell erwärmen / ausdehnen.
Anmerkung:
Beim Feuerverzinken werden die aus dem Bearbeitungsprozess (Biegen, Richten, Strecken, Stauchen, Schweißen usw.) herrührenden Materialeigenspannungen teilweise wieder abgebaut (Beruhigung durch Wärmebehandlung). Das kann Formänderungen bewirken. Deshalb sind sogar lose Bleche verzugsgefährdet - wurden diese bei der Herstellung doch häufig kalt gewalzt oder gerichtet!
Normen
Die korrosionsschutz- und feuerverzinkungsgerechte Gestaltung von Stahlteilen ist Gegenstand der Norm*:
"Schutz von Eisen- und Stahlkonstruktionen vor Korrosion - Zink- und Aluminiumüberzüge - Leitfäden"
DIN EN ISO 14713
Die Regelungen zu den Zinküberzugs-Eigenschaften enthält die Norm*:
"Durch Feuerverzinken auf Stahl aufgebrachte Zinküberzüge (Stückverzinken) - Anforderungen und Prüfungen"
DIN EN ISO 1461:2009
*Zu beziehen über: BEUTH-Verlag GmbH, Burggrafenstr 6, 10787 Berlin